>> Differential
speed regulation
>>> General
see
table IV
There are two basic regulation models, digital and analog. The
digital regulation permits a hand adjustable, fixed differential
speed, which will 'boost' the differential speed to the maximum
at some variable preset pressure (scroll torque). The analog regulation
permits a hand adjustable fixed differential speed (so-called base
speed delta n), and a gradual increase in differential speed as
pressure (scroll torque) increases. The point at witch the differential
speed increases, called the regulation point (P1) is variable, and
the rate of increase (a) is also adjustable. Table IV shows the
analog regulation. With both analog and digital regulation, safety
cut-outs are provided in the case of high torque (P2) and very high
torque (P3). These are signaled by pressure switches (adjustable)
and are usually set-up to cut out the feed pump at (P2) and cut-off
the bowl drive ant (P3). A pressure relief valve protects the system
from overload, preventing damage to the scroll drive by over torque.
This is at a higher value than P3, and has the effect of maintaining
maximum torque on the scroll so that, as the bowl runs down in speed,
the falling 'G' forces will often allow the scroll to commence rotation
again and 'unplug' a blocked machine.
Note:
Some incompressible products do not respond well to analog regulation,
since an increase in differential causes an increase in scroll torque,
rather than a decrease. In these cases it is advisable to use digital
operation, and the analog regulation can in most cases be set to
operate in a digital mode, when a = minimum, and P1 is set at a
high value.
>>> Hydrostatic regulation systems
see
table IV
A specific control block can be mounted on the tank top, according
to the required mode. The hydrostatically regulated control block
(P3H) uses the direct feedback of variable pressure i.e. variable
scroll torque. The regulation characteristic are adjustable through
three hydrostatic valves (see table IV), the emergency functions
are set on a manometer pressure gauge and switch. Such systems are
advantageous for their easy operation and reliability.
>>> Electronic regulation systems
A proportional valve mounted on the control block (P3E) controls
the pump unit oil flow to the scroll drive (R). The control current
on the proportional valve coil corresponds directly with the oil
flow to the scroll drive motor (R). Also mounted on the control
block is an electronic pressure transmitter which signals the measured
pressure on the electronic display and control unit (E). The electronic
display and control unit shows the following:
|
Differential speed (with pick up sensor) |
|
Bowl speed (with pick up sensor) |
|
Hydraulic pressure (over pressure transmitter) |
The three regulation parameters are easily adjustable through
potentiometers on the electronic unit (E).
The advantage of such electronic regulation systems are:
|
A precise regulation within the lower range of the differential
speeds is possible. |
|
Can be integrated into lager cybernetic systems. |
If a CVC unit is used, then the following additional advantages
are:
|
Through feedback of the measured differential speed an operation
within extremely low differential speed is possible. (Monitoring
of the differential speed through a closed loop control circuit).
|
|
Pre-stored regulation curves can be used. (Non linear regulation
characteristic modes are possible) |
|
Utilization of additional regulation parameters are possible
(Feed rate, flocculation and so on) |
|
Storage of working parameters (Journal) |
|
Visualization of regulation characteristics on a screen. |
|
Table l
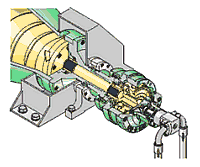
Table ll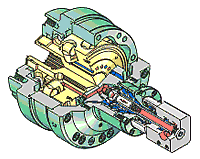
Table IV
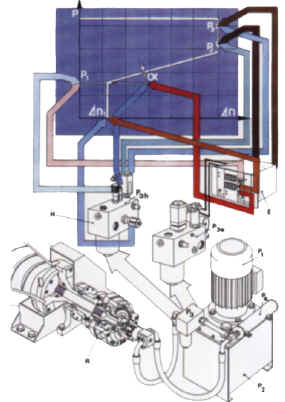
|