>> Rotodiff
>>> Components
The hydrostatic slip drive consists of the following components:
see
table IV
|
The slow speed high torque hydraulic scroll drive motor (R)
ROTODIFF, is a rotating unit. |
|
The Pump Unit (P), mounted on the floor, near Rotodiff. |
|
A control system either (H) hydrostatic or (E) electronic
control. |
>>> The hydraulic scroll drive motor ROTODIFF
see
table l
>>>> General:
The Rotodiff housing is directly bolted to the centrifuge bowl and
the drive shaft is joined to the centrifuge scroll like a normal
gear box. The Rotodiff mounted on the centrifuge rotor and, together
with a Pump unit, comprises the complete drive system.
The Rotodiff (R) is a slow speed, high torque hydraulic motor with
a constant displacement. The housing is flanged to the decanter
bowl, and the Rotor (R6) drives the decanter scroll (C1). In this
way, the scroll is driven at an adjustable differential speed, independently
of the bowl speed. The high pressure hydraulic oil (red path) is
brought from the stationary part (R3), to the rotating part of the
motor (R6), by means of the transfer seal (R2). The unpressurized
hydraulic oil (blue path), flows back to the pump unit over the
stationary part (R3).
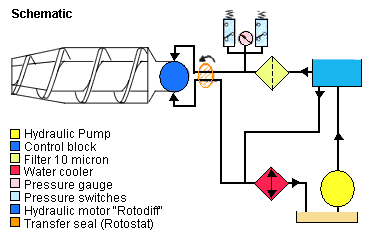
>>>> Working principal of the hydraulic motor
see
table II
The hydraulic motor is a positive displacement radial piston motor.
The cam (R4) transmits the force exerted by the piston rollers (R8)
through pressure from the pistons (R7). The tangential component
of this force produces the rotation of the rotor (R6). The pistons
in the cylinder are subject to fluid under pressure via the distributor
(R5) which is mechanically linked to the cam. The cylinders are
thus alternately connected to the high pressure of the hydraulic
feed system (working stroke; red path) and the low pressure of the
casing (return stroke; blue path).
>>>> Working principal of the transfer seal
see
table II
This element is critical for the function of the hydraulic motor.
It has the ensure a very low leakage rate under highest pressures,
and must have a adequate passage for the high pressure oil flow
as well as extremely low friction loss. A ball cone (R9) is placed
on the rotating part eccentrically, and is connected via a double
cone floating eccentric ring (R10) to the stationary, compensation
cap (R11). The rotating ball cone and stationary compensation cap
(parts R9 + R11) cause a tumbling motion of the floating eccentric
ring, which continually laps and polishes the contracting surfaces.
A considerable axial force is generated between the stationary and
the rotating part. This axial force is contained by the two angular
ball bearings (R12).
|
Table l
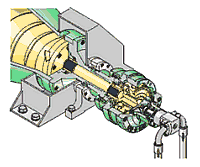
Table ll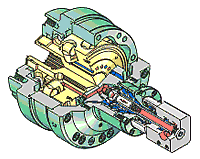
Table IV
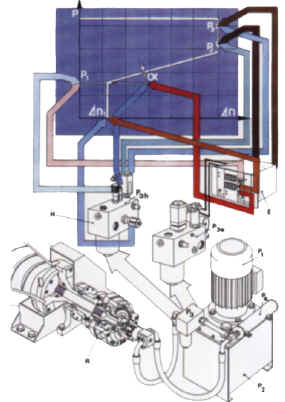
|